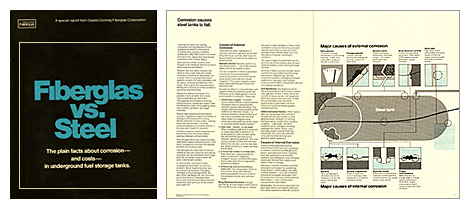
At the time this piece was produced, the underground fuel storage market was dominated by steel tanks and Owens-Corning was just beginning to
produce a corrosion-resistant but more expensive fiber glass tank. As a result of a number of highly publicized
steel tank failures due to corrosion and the resulting gasoline contamination of surrounding soil and ground water,
the future of fiber glass suddenly seemed brighter. We were given the job of researching and collecting the data on corrosion from many technical sources and compiling it into a compelling story for fiber glass.
The result was this 8 page
brochure, essentially a white paper on the causes
of underground corrosion leading to steel tank failure.
The ultimate selling point was one of cost; the expense of adding active or passive cathodic protection to steel tanks to prevent corrosion (or their periodic replacement) more than offset the additional cost of
the more exacting
burial process for the more fragile fiber glass tanks. The piece was widely distributed to the trade and general media. Given the huge liability downside
of tank failure and the new lower cost of fiber glass, Owens Corning tanks soon became the virtual default choice for underground storage of sensitive
fluids.

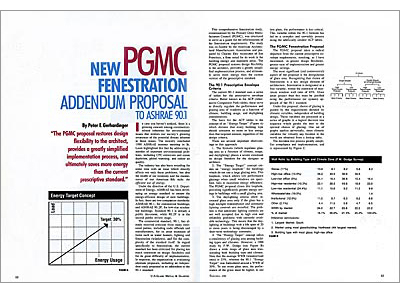
This technical article in
U.S. Glass, Metal & Glazing magazine was authored under the name of our client, Pete Gerhardinger, an engineer at LOF. The contents were also prepared as a speech he gave to a summer meeting of ASHRAE, a construction industry association. Under the direction of the U.S. Department of Energy, ASHRAE was at this time developing a new set of energy standards in building construction, including fenestration (windows), to save energy and reduce environmental degradation. LOF, as a leading manufacturer of window glass, felt the standards reduced the flexibility of fenestration too greatly and were too difficult to implement. The content of this article is a proposal for a revised fenestration standard which would be more flexible and save more energy.

Our client, J.B.Martin, the world's largest producer of velvet fabric, asked us to help transfer their multi-layer fabric technology to the advanced composite market, where multi-layer fabrics could substantially reduce hand labor costs in the manufacture of high end aerospace components. This four page technical brochure describes the fabric architecture of Martinply, a non-crimp, multi layered, multi-directional woven fabric. The objective was to sell not only Martinply, but the company's capability to produce custom engineered fabric structures at reasonable cost/performance levels to meet the needs of specific high end applications.